Prof. Dominic Eggbeer Publications
PDR Research
- Focus:
- Surgical Prosthetic Design
Identifying research and development priorities for an in-hospital 3D design engineering facility in India
Eggbeer, D., Mehrotra, D., Beverley, K., Hollisey-McLean, S. and Evans, P. (2020) 'Identifying research and development priorities for an in-hospital 3D design engineering facility in India', Journal of Design, Business & Society, 6(2), pp.189-213. https://doi.org/10.1386/dbs_00011_1
Advanced three-dimensional (3D) design and engineering technologies have revolutionized patient-specific implants, prostheses and medical devices, particularly in the cranio-maxillofacial and oral medical fields. Lately, decreasing costs, coupled with the reported benefits of bringing design and production technology closer to the point of healthcare delivery, have encouraged hospitals to implement their own 3D design and engineering services. Most academic literature reports on the factors that influence the sustainable development of such services in high-income countries. But what of low- and middle-income countries where demand for custom craniofacial devices is high? What are the unique challenges to implement in-hospital services in resource-constrained environments? This article reports the findings of a collaborative project, Co-MeDDI (Collaborative Medical Device Design Initiative), that brought together a UK-based team with the experience of setting up and running a hospital-based 3D service in the United Kingdom with the Maxillofacial Department of a public hospital in the Uttar Pradesh region of India, which had recently received funding to establish a similar capability. We describe a structured design research approach consisting of a series of exchange activities taking place during the lifetime of the project that compared different aspects of the healthcare innovation ecosystem for 3D services in India and the United Kingdom. Based on the findings of the different activities, we identify key factors that influence the adoption of such services in India. The findings are of relevance to healthcare policy-makers and public hospital managers in resource-constrained environments, and to academics and practitioners engaging in collaborative export of healthcare initiatives.
Find more information here: https://doi.org/10.1386/dbs_00011_1
Uncovering self-management needs to better design for people living with lymphoedema
Kopanoglu,Teksin, Beverley, Katie, Eggbeer, Dominic & Walters, Andrew (2019) 'Uncovering self-management needs to better design for people living with lymphoedema', Design for Health, 3 (2), pp. 220-239, DOI: 10.1080/24735132.2019.1686326
This paper reports on the application of design-based tools used to uncover the needs of people living with a chronic condition. It was built on increasing rhetoric calling for greater involvement of patients in the creation of appropriate support mechanisms and presents a means to achieve this using design approaches and tools. The paper presents the development and use of scenario-based design probes to facilitate the participation of People Living with Lymphoedema (PLWL) early in the design process. Lymphoedema is a chronic condition requiring a cumbersome everyday management routine. Self-management is necessary to increase quality of life and decrease complications and hospitalisation. However, consistent practice of self-management among PLWL is low and the need to improve support is recognised. This research explored how PLWL’s transitions towards becoming experts of their condition might be supported. Literature describing the lymphoedema experience was systematically investigated from a behavioural perspective to develop scenario-based probes. These probes provided rich insights by facilitating the envisioning of alternative futures to self-management support with interview participants with lymphoedema. To inform the design of better support for chronic conditions, the stages and components of behaviour change for lymphoedema self-management and the associated support needs are presented.
Find more details here: https://doi.org/10.1080/24735132.2019.1686326
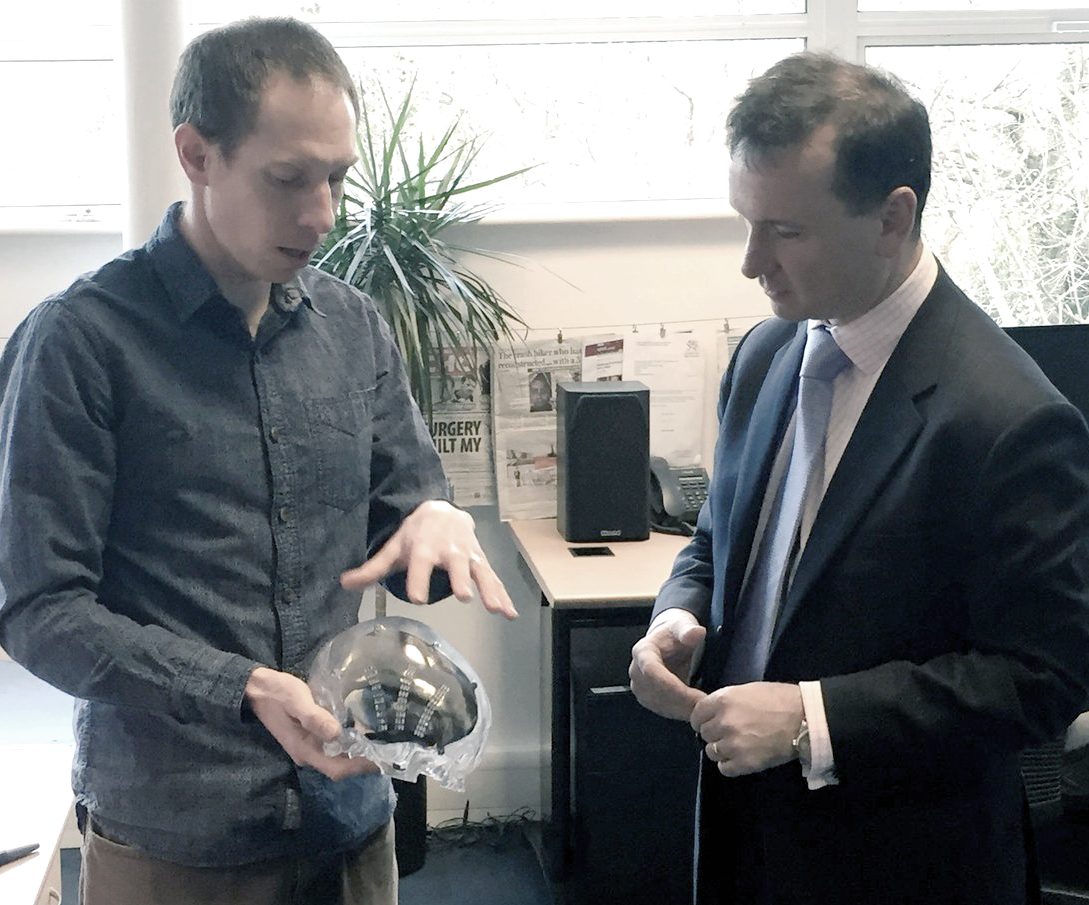
Evaluating additive manufacturing for the production of custom head supports: A comparison against a commercial head support under static loading conditions
Howard, J.D., Eggbeer, D., Dorrington, P., Korkees, F. and Tasker, L.H. (2020) 'Evaluating additive manufacturing for the production of custom head supports: A comparison against a commercial head support under static loading conditions', Proceedings of the Institution of Mechanical Engineers, Part H: Journal of Engineering in Medicine, p.0954411919899844. DOI: 10.1177/0954411919899844.
The provision of wheelchair seating accessories, such as head supports, is often limited to the use of commercial products. Additive manufacturing has the potential to produce custom seating components, but there are very few examples of published work. This article reports a method of utilising 3D scanning, computer-aided design and additive manufacturing for the fabrication of a custom head support for a wheelchair. Three custom head supports, of the same shape, were manufactured in nylon using a continuous filament fabrication machine. The custom head supports were tested against an equivalent and widely used commercial head support using ISO 16840-3:2014. The head supports were statically loaded in two configurations, one modelling a posterior force on the inner rear surface and the other modelling a lateral force on the side. The posterior force resulted in failure of the supporting bracketry before the custom head support. A similar magnitude of forces was applied laterally for the custom and commercial head support. When the load was removed, the custom recovered to its original shape while the commercial sustained plastic deformation. The addition of a joint in the head support increased the maximum displacement, 128.6 mm compared to 71.7 mm, and the use of carbon fibre resulted in the head support sustaining a higher force at larger displacements, increase in 30 N. Based on the deformation and recovery characteristics, the results indicate that additive manufacturing could be an appropriate method to produce lighter weight, highly customised, cost-effective and safe head supports for wheelchair users.
Find more information here: https://doi.org/10.1177/0954411919899844
Computer-aided methods for single stage fibrous dysplasia excision and reconstruction in the zygomatico-orbital complex
Budak, I., Kiralj, A., Sokac, M., Santosi, Z., Eggbeer, D. and Peel, S. (2019) 'Computer-aided methods for single-stage fibrous dysplasia excision and reconstruction in the zygomatico-orbital complex', Rapid Prototyping Journal. DOI: 10.1108/RPJ-05-2018-0116.
Computer Aided Design and Additive Manufacture (CAD/AM) technologies are sufficiently refined and meet the necessary regulatory requirements for routine incorporation into the medical field, with long-standing application in surgeries of the maxillofacial and craniofacial region. They have resulted in better medical care for patients, and faster, more accurate procedures. Despite ever-growing evidence about the advantages of computer aided planning, CAD and AM in surgery, detailed reporting on critical design decisions that enable methodological replication, and the development and establishment of guidelines to ensure safety, are limited. This paper presents a novel application of CAD and AM to a single stage resection and reconstruction of fibrous dysplasia in the zygoma and orbit. It is reported in sufficient fidelity to permit methods replication and design guideline developments in future cases, wherever they occur in the world. The collaborative approach included engineers, designers, surgeons and prosthetists to design patient-specific cutting guides and a custom implant. An iterative design process was used, until the desired shape and function were achieved, for both of the devices. The surgery followed the CAD plan precisely and without problems. Immediate post-operative subjective clinical judgements were of an excellent result. At 19 months post-op, a CT scan was undertaken to verify the clinical and technical outcomes. Dimensional analysis showed maximum deviation of 4.73 mm from the plan to the result, while CAD-Inspection showed that the deviations range between -0.1 and -0.8 mm, and that the majority of deviations are located around the –0.3 mm. Improvements are suggested and conclusions drawn regarding the design decisions considered critical to a successful outcome for this type of procedure in the future.
Find more information here: https://doi.org/10.1108/RPJ-05-2018-0116
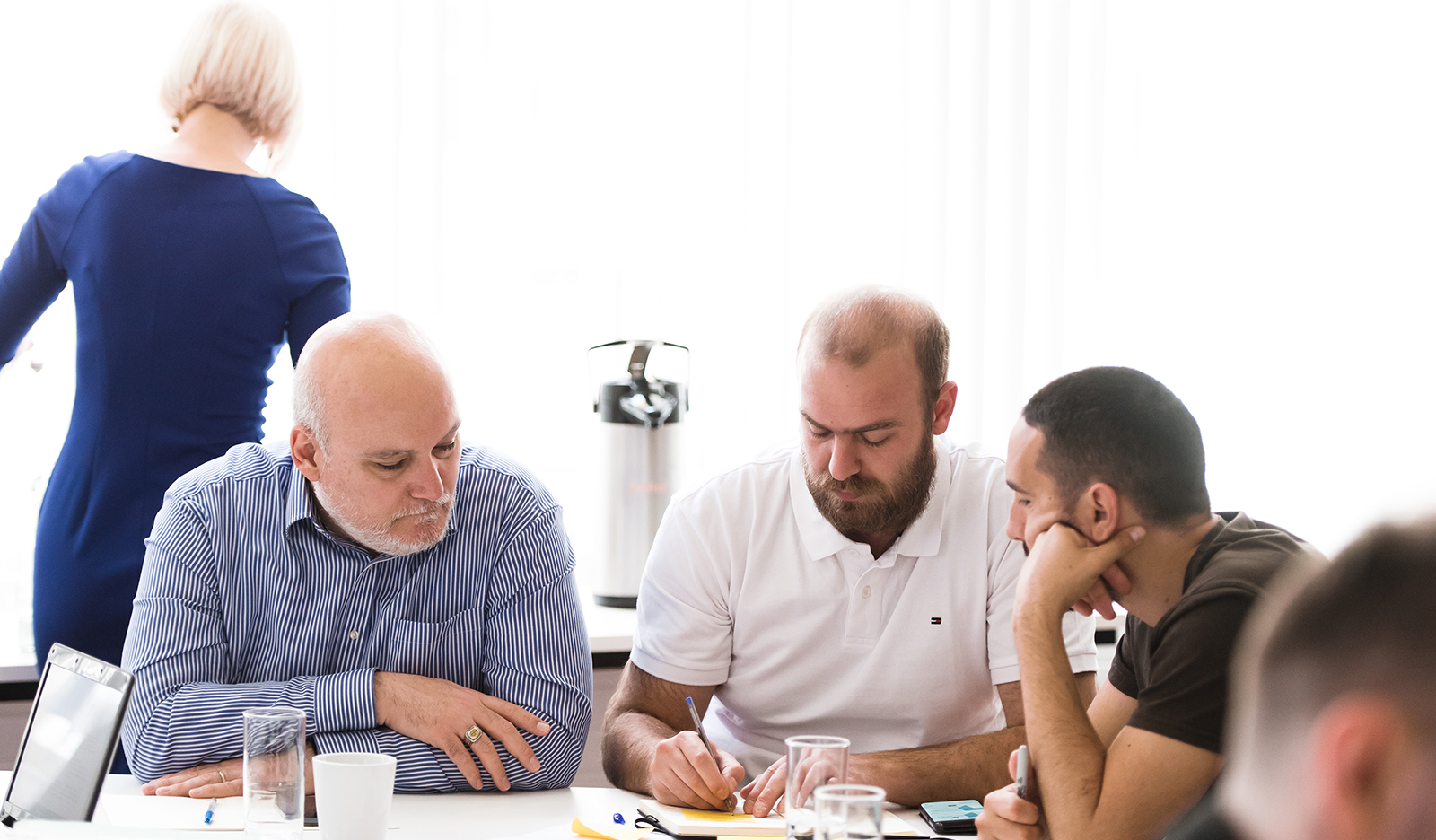
Comparative analysis of structure and hardness of cast and direct metal laser sintering produced Co-Cr alloys used for dental devices
Lapcevic, A.R., Jevremovic, D.P., Puskar, T.M., Williams, R.J. and Eggbeer, D. (2016) 'Comparative analysis of structure and hardness of cast and direct metal laser sintering produced Co-Cr alloys used for dental devices', Rapid Prototyping Journal, 22(1), pp.144-151. DOI: 10.1108/RPJ-04-2014-0051.
Purpose: The purpose of this paper is to analyse structure and measure hardness of Co-Cr dental alloy samples made with two different technologies, conventional casting method (CCM samples) and additive direct metal laser sintering technology (DMLS samples), and to compare the results. Design/methodology/approach: CCM samples were made in a conventional casting machine, using remanium 800+ Co-Cr dental alloy (Dentaurum, Ispringen, Germany). DMLS samples were fabricated out of EOS CC SP2 Co-Cr alloy (EOS, GmbH, Munich, Germany) using DMLS technology. Samples for structural analysis were plate-shaped (10 × 10 × 1.5 mm3) and for the hardness test were prismatic-shaped (55 × 10.2 × 11.2 mm3). Structure was analysed via an inverting microscope and colour metallography method. Findings: CCM samples have a dense, irregular dendritic mesh, which is typical for the metallic phase of the Co-Cr dental alloy. DMLS alloy has a more homogenous and more compact structure, compared to CCM. Metals, the alloy basis consists of, form semilunar stratified layers, which are characteristic for the additive manufacturing (AM) technique. Hardness values of DMLS (mean value was 439.84 HV10) were found to be higher than those of CCM (mean value was 373.76 HV10). Originality/value: There are several reports about possible use of AM technologies for manufacturing dental devices, and investigation of mechanical properties and biocompatibility behaviour of AM-produced dental alloys. Microstructure of Co-Cr alloy made with DMLS technology has been introduced for the first time in the present paper.
Find more information here: https://doi.org/10.1108/RPJ-04-2014-0051
Medical Modelling: The Application of Advanced Design and Rapid Prototyping Techniques in Medicine (Woodhead Publishing Series in Biomaterials)
Bibb R., Eggbeer D., Paterson A. (2015) Medical Modelling: The Application of Advanced Design and Rapid Prototyping Techniques in Medicine., 2nd Edition. Cambridge: Woodhead Publishing
Medical modelling and the principles of medical imaging, Computer Aided Design (CAD) and Rapid Prototyping (also known as Additive Manufacturing and 3D Printing) are important techniques relating to various disciplines - from biomaterials engineering to surgery. Medical Modelling: The application of Advanced Design and Rapid Prototyping techniques in medicine provides readers with a revised edition of the original text, along with key information on innovative imaging techniques, Rapid Prototyping technologies and case studies. Following an overview of medical imaging for Rapid Prototyping, the book goes on to discuss working with medical scan data and techniques for Rapid Prototyping. In this second edition there is an extensive section of peer-reviewed case studies, describing the practical applications of advanced design technologies in surgical, prosthetic, orthotic, dental and research applications.
Find more information here: https://www.sciencedirect.com/book/9781782423003/medical-modelling
Computational design of biostructures
Eggbeer, D. (2017) 'Computational design of biostructures', In Thomas, D., Jessop, Z. & Whitaker, I. (ed.s) 3D Bioprinting for Reconstructive Surgery: Techniques and Applications (Woodhead Publishing Series in Biomaterials) Cambridge: Woodhead Publishing. pp.33-74.
The application of medical imaging, Computer Aided Design (CAD) and Additive Manufacturing (AM) in the field of biostructures is evolving at a rapid pace. Upon its initial conception in the 1980s through to the 1990s, CAD and AM were largely developed for the aerospace, automotive and other engineering sectors. As technologies became more commercialised and affordable, bureau services began adopting them, making them more widely available in product development. In parallel to other industrial sectors, interest in the application of advanced computer-based technologies to medical applications has also grown dramatically, particularly in the last two decades. This has been driven by advances in medical imaging modalities, such as Computer Tomography (CT), improvements in specifically developed CAD software and increased accessibility of high performance computer technologies.
Find more information here: https://www.sciencedirect.com/book/9780081011034/3d-bioprinting-for-reconstructive-surgery
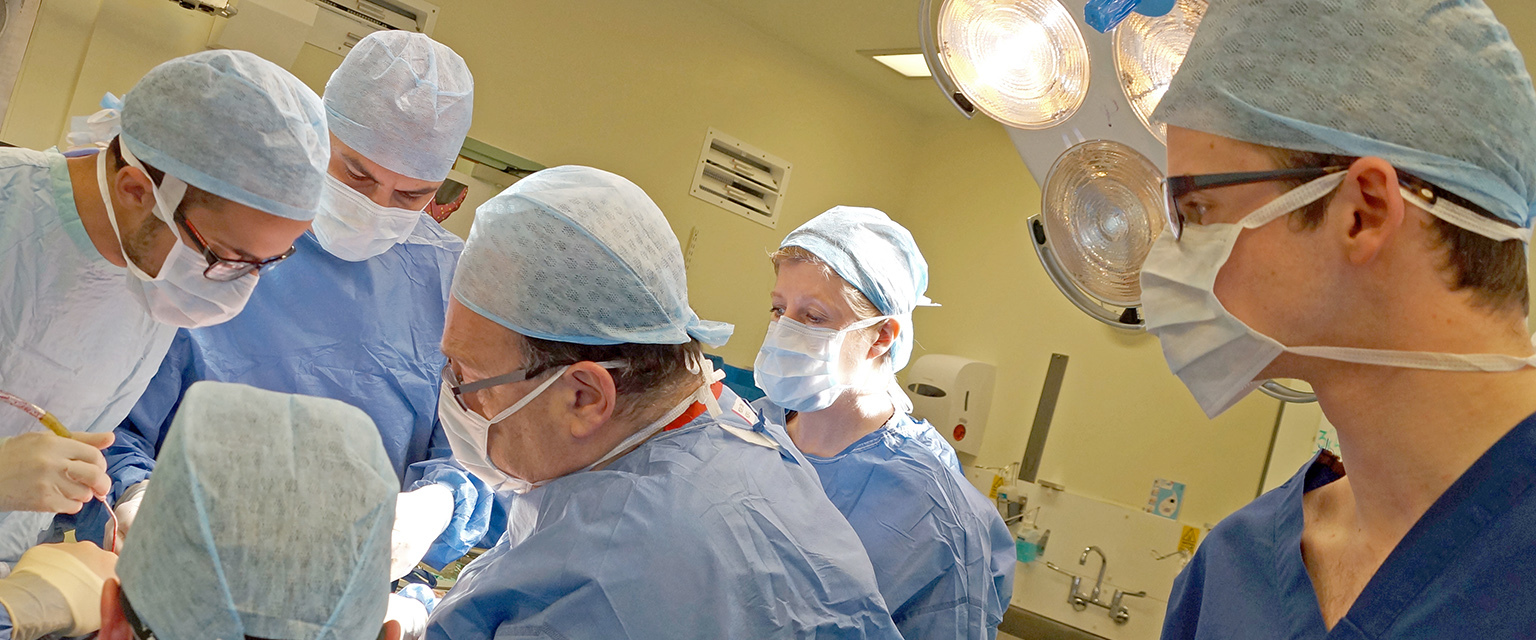
Additively manufactured versus conventionally pressed cranioplasty implants: An accuracy comparison
Peel, S., Eggbeer, D., Burton, H., Hanson, H. and Evans, P.L. (2018) 'Additively manufactured versus conventionally pressed cranioplasty implants: An accuracy comparison', Proceedings of the Institution of Mechanical Engineers, Part H: Journal of Engineering in Medicine, 2018, 0954411918794718.
This article compared the accuracy of producing patient-specific cranioplasty implants using four different approaches. Benchmark geometry was designed to represent a cranium and a defect added simulating a craniectomy. An ‘ideal’ contour reconstruction was calculated and compared against reconstructions resulting from the four approaches –‘conventional’, ‘semi-digital’, ‘digital – non-automated’ and ‘digital – semi-automated’. The ‘conventional’ approach relied on hand carving a reconstruction, turning this into a press tool, and pressing titanium sheet. This approach is common in the UK National Health Service. The ‘semi-digital’ approach removed the hand-carving element. Both of the ‘digital’ approaches utilised additive manufacturing to produce the end-use implant. The geometries were designed using a non-specialised computer-aided design software and a semi-automated cranioplasty implant-specific computer-aided design software. It was found that all plates were clinically acceptable and that the digitally designed and additive manufacturing plates were as accurate as the conventional implants. There were no significant differences between the additive manufacturing plates designed using non-specialised computer-aided design software and those designed using the semi-automated tool. The semi-automated software and additive manufacturing production process were capable of producing cranioplasty implants of similar accuracy to multi-purpose software and additive manufacturing, and both were more accurate than handmade implants. The difference was not of clinical significance, demonstrating that the accuracy of additive manufacturing cranioplasty implants meets current best practice.
Find more information here: https://doi.org/10.1177/0954411918794718
Reporting fidelity in the literature for computer aided design and additive manufacture of implants and guides
Burton, H.E., Peel, S. and Eggbeer, D. (2018) 'Reporting fidelity in the literature for computer aided design and additive manufacture of implants and guides', Additive Manufacturing, 23(October)
The aim of this study was to critically evaluate the nature and reporting fidelity of literature about applications of computer aided design (CAD) and metal additive manufacture (AM) to surgical guides and implants. Increasingly, non-specialist designers such as surgeons or prosthetists are partaking in some or all of the design process. To comply with local regulations, it is imperative that quality is ensured during the design process, yet it is rare for literature to report on the design process of medical devices with sufficient detail to allow proper evaluation or reproduction. This study reviewed the CAD/AM literature for implant and guide design, focusing on detailed justifications for design decisions, economic impacts, and production methods. This review showed that the fidelity of reporting in the literature was low; with opportunities to report crucial design decisions, engineering parameters, and how these relate to clinical results being frequently missed. This research proposes the low fidelity in reporting is likely due to a combination of: reporting for different specialisms, resulting in a lack of expert knowledge in certain areas and assumed knowledge in others; commercial sensitivity of design and manufacturing methods; low volume of clinical cases; and a large gap in translating research to clinical applications. This study concluded that higher fidelity in reporting methods are required when discussing the design of AM medical implants, which would allow comparisons between studies, provide evidence to support design quality, and enable evidence-based decision-making.
Find more information here: https://doi.org/10.1016/j.addma.2018.08.027